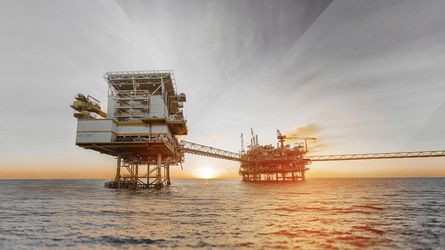
Oil & Gas
You can rely on 60 years of experience in the construction of pumps, packages, skids, and systems for onshore and offshore oil and gas production. Take a look at the information now!
Read more
The advantages of LEWA diaphragm metering pumps and packages in the injection of corrosion inhibitor:
Process description
A distinction is made between anodic and cathodic corrosion inhibitors.
Cathodic corrosion inhibitors are mainly used for oil and gas production.
In the offshore industry, production sites are being driven into increasingly deeper water. This increases the discharge pressure. While 160-250 bar are sufficient onshore, the offshore pressure is often above 900 bar. The flow rate is normally around 50 l/h. Injection is continuous.
Possible chemical reactions must be detected and accounted for:
The components of crude oil cause corrosion and scale deposits. The injection of corrosion and scale deposit inhibitors helps. Limited success is achieved by using a combination of these additives, since both chemicals neutralize and are rendered inactive.
It should therefore be checked whether a reduction of the injection volume of the corrosion inhibitor could lead to a residual acidic content in the crude oil, which would destroy the scale deposits anyway.
Central distribution of corrosion inhibitors:
If several injection points are supplied with corrosion inhibitors at a central location, the use of flow dividers must be considered. This requires only the installation of one large pump to provide the entire flow and a multiple distributor system.
The flow is distributed via small valves and pressure compensating devices and delivered to the various injection points. However, the space requirements only appear to be better, since in actuality each injection point requires a separate control system. Moreover, the injected fluid must be very pure, since otherwise the pressure compensation valves, which have very tight tolerances, can get stuck.
Highly pure fluids and very small components are very sensible to fluctuations in viscosity and pressure.